Customer Success Story
With Predictive Maintenance
As a global manufacturing hub, it is essential that the Schaeffler plant in Bien Hoa City, Vietnam, remains operational at all times. It is therefore, crucial that the machines are kept in optimal working condition in order to prevent any unplanned downtime. With this in mind, a holistic conditioning monitoring solution was implemented to help keep the machines in optimum working order and thereby minimize the risk of breakdowns that may have detrimental business consequences.
The bottom line after eight months: Annual saving of 50,000 euros, a 30% reduction in maintenance effort and 0 downtimes since the introduction of the predictive maintenance solution.
Benefits
Reduced maintenance costs
Lower risk of unplanned downtime
Intelligible data for diagnosis
Enhanced planning of resources and inventory
Support readily available for diagnosis by Schaeffler Experts
Challenge
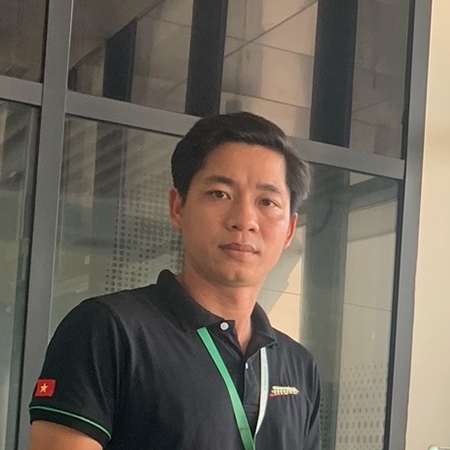
Solution - Summary
Following consultation with Schaeffler experts in both Asia Pacific and Germany, the maintenance team at the Vietnam plant decided to implement a thorough and holistic condition monitoring solution consisting of SmartCheck for critical motors, fans, and pumps, a ProLink CMS system for compressors, and an OPTIME system to complete the monitoring of the remaining auxiliary machines. Lastly, the lubrication of critical motors and pumps was handled by the CONCEPT1 automatic lubricators, to ensure that critical machines remained well lubricated and in optimum condition at all times.
Monitoring of Critical Machines – SmartCheck
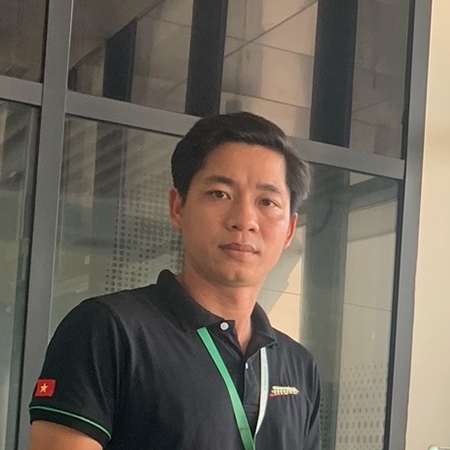
Monitoring of Compressors - ProLink CMS
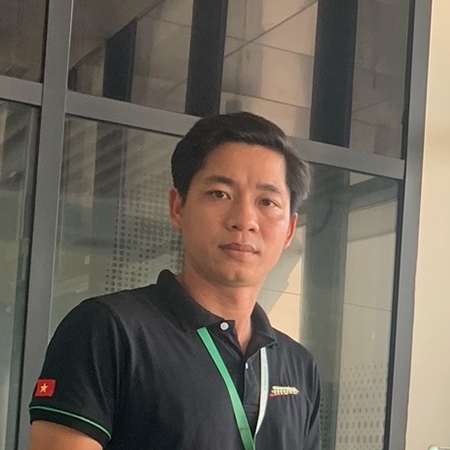
Monitoring of Auxiliary Machines – OPTIME
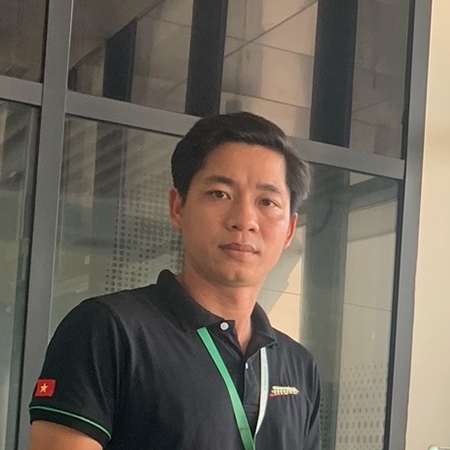
Lubrication of Critical Machines – CONCEPT1
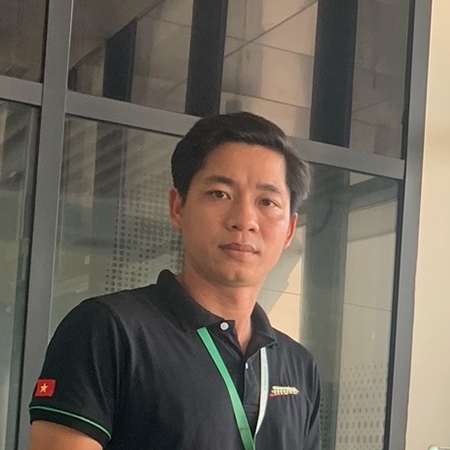